Technique : La roue
le 03/08/2005
La tradition courante, faute d'éléments précis, attribue l'invention de la roue à une série de constatations des plus élémentaires dues au hasard, telles que le fait qu'un objet roule plus facilement lorsqu'il est de forme ronde, aux plus complexes : en faisant glisser un poids sur des troncs d'arbres, on supprime le frottement. Cette seconde façon de procéder, qui remonte aux débuts de la civilisation, semble être à l'origine de la roue actuelle quoique le passage du tronc d'arbre à la roue considérée comme un dispositif qui, utilisé de façon permanente, permet de déplacer plus facilement un objet lourd, ne soit absolument pas une déduction logique, mais fasse intervenir « une science ». Certains peuples évolués connaissaient l'emploi de la roue depuis des millénaires (comme le prouvent les découvertes archéologiques d'Ur que l'on fait remonter à 3500 ans av. J:C.) tandis qu'elle restait totalement inconnue des Incas lorsque ces derniers entrèrent en contact avec la civilisation occidentale, cinq mille ans plus tard. Du point de vue mécanique. la roue est caractérisée par le moyeu.
Cet organe est fixe, solidaire de l'objet à déplacer et en supporte tout le poids qu'il transfère au sol à travers la partie mobile de la roue. La fonction de cette "machine" consiste à transférer le frottement de glissement de la zone de contact avec le sol (où il devient frottement de roulement. mais d'une valeur bien inférieure) à une zone plus petite, représentée par le moyeu au niveau duquel on enregistre des vitesses relatives très inférieures (les vitesses sont proportionnelles au rayon). Enfin, sur la fusée il est plus facile d'obtenir les conditions nécessaire pour faire tourner la roue est sensiblement inférieure à l'énergie requise pour la faire glisser sur le sol.
Ce principe, présence de surfaces lisses, dures, et surtout la possibilité de graissage, font que l'énergie nécessaire pour faire tourner la roue est sensiblement inférieure à l'énergie requise pour faire glisser la roue sur le sol. Ce principe n'est toutefois pas valable lorsque le frottement de roulement entre la roue et le sol a tendance à s'annuler ou lorsque le frottement de glissement sur certaines surfaces est insignifiant (aquaplaning ou marche sur glace).
Dans ces cas il est même possible que la roue cesse de tourner, le frottement entre cette dernière et le sol s'avérant insuffisant pour vaincre la résistance au roulement. C'est pourquoi, pour se déplacer sur la glace, on préfère utiliser des patins plutôt que les roues. La résistance de la roue au roulement est due non seulement au frottement se produisant au niveau du moyeu mais également au frottement du diamètre de la roue : plus le diamètre est grand et moins le frottement de roulement est important. Dans la pratique toutefois, les choses n'obéissent pas à cette règle.

D.R.
En effet, la zone de contact entre une surface plane et un disque n'est que théoriquement représentée par une ligne droite parallèle à l'axe de rotation: en réalité, les matériaux venant en contact ne sont pas absolument rigides et il se produit toujours un aplatissement plus ou moins important dans la zone d'appui, sur laquelle est répartie la charge verticale. La surface de contact est le résultat d'une déformation (de la roue, du terrain, ou des deux) qui nécessite un certain travail pour se produire.
Pendant la marche, des déformations se succèdent sans interruption, qui intéressent toute la circonférence de la roue et son parcours. Ces déformations sont en partie permanentes (le sol s'écrase et l'empreinte persiste après le passage) et en partie élastiques (une roue garnie d'un pneumatique fléchit lorsqu'elle est en charge et reprend ensuite sa forme originale).
Dans la partie arrière, par contre, se vérifie une pression sensiblement inférieure. La répartition des pressions sur la zone de contact est indiquée dans un schéma. La résultante (toujours égale au poids vertical) ne passe plus, cette fois, par le centre de la roue, mais se trouve déplacée vers l'avant (dans le sens du mouvement). Cette résultante crée un moment résistant par rapport à l'axe de la roue, qui représentera le couple qu'il faut appliquer pour actionner la roue elle-même. Sa valeur dépend de la charge s'exerçant sur la roue, de son diamètre, de la vitesse de la voiture et de la nature des matériaux de la surface de contact. Ce déplacement vers l'avant de la résultante se vérifie toujours, que la roue soit tractée ou motrice, ou encore qu'elle soit freinée. Lorsque la roue, à l'arrêt, est soumise à une force latérale, la flexibilité du pneumatique provoque un déplacement latéral de la surface qui sera proportionnel à l'adhérence et à la rigidité du pneumatique.
Pendant le roulement d'une roue en caoutchouc, la pression n'est pas uniforme et la résultante de la réaction du terrain est appliquée à l'avant par rapport à la verticale qui passe par le centre de la roue (point d'application du poids)...
...le couple qui en résulte est celui qu'il faut vaincre pour faire rouler le pneumatique. L'adhérence latérale, par contre, (ci dessus), sous l'effet de la dérive qui, pour une roue non motrice, déplace vers l'arrière la surface d'empreinte, est appliquée à l'arrière.
C'est un des éléments qui contribuent à redresser la roue dans les courbes.
Dans les virages, le phénomène est plus complexe, car, en plus des variations de pression sur la surface de contact occasionnées par le roulement lui-même, d'autres phénomènes se produisent et, en premier lieu, la « dérive ».
En effet, la direction du mouvement ne coïncide pas avec celle de la jante ; la résultante de la réaction du terrain sur la zone de contact (en l'occurrence l'adhérence latérale) n'est pas directement perpendiculaire à la roue mais à la trajectoire.
Cette orientation détermine une composante (tangentielle à la trajectoire) tournée vers l'arrière qui tendra à ralentir la marche de la voiture en provoquant en même temps une distorsion de la zone de contact (qui se trouve ainsi tirée vers l'arrière). Elle est d'autant plus grande que la dérive est importante.
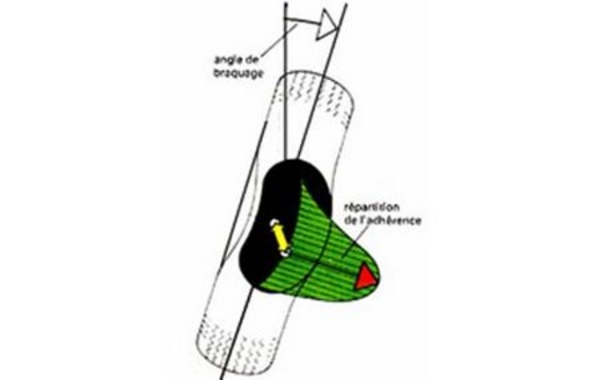
D.R.
La résultante de l'adhérence totale est donc appliquée derrière l'axe de la roue, disposition à l'origine d'un moment d'auto-alignement de la roue, qui tendra à la ramener sur sa trajectoire effective. Ce phénomène est uniquement valable pour la roue « folle »; pour la roue motrice, en effet, l'effort de traction, dirigé dans le même sens que la jante, a une composante longitudinale qui tend à ramener vers l'avant la zone de contact.
Les déformations et les déplacements de la surface de contact, causés par la souplesse du pneumatique, sont plus sensibles dans le cas des voitures qui ont un déport positif très faible ; en effet, la distorsion de la bande de roulement vers l'intérieur de la courbe fait que, pour des angles de braquage importants, je déport effectif (c'est-à-dire la distance entre l'axe de pivot et le point d'application de l'adhérence) s'annule ou devient même négatif, ce qui provoque des anomalies dans les réactions qui se vérifient pendant la conduite.
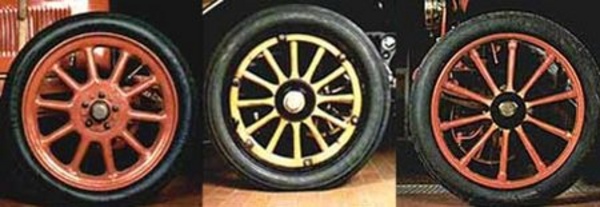
Roue en bois et renforts métalliques (1900), roue en bois avec jante démontable (1900), roue Sankey entièrement métallique (1920) D.R.
Depuis ses premières applications, la roue a subi une évolution surtout stylistique pour respecter les canons de l'esthétique des diverses époques ; par contre, en ce qui concerne sa structure elle est restée, pendant longtemps, inchangée : roue en bois à rais, souvent avec des bandages et des moyeux renforcés par un cerclage métallique.
Ce n'est qu'après 1943, à la suite de l'invention de la vulcanisation du caoutchouc, que l'on commença à remplacer les cerclages en fer par des bandages en caoutchouc plein, de façon à amortir les vibrations et les chocs légers causés par les irrégularités de la chaussée. Cette technique prévalut jusqu'aux premières années du XXème siècle, bien que la fabrication des pneumatiques ait commencé dés 1885. Mais la production de l'époque suffisait à peine à répondre aux besoins de l'équipement des véhicules légers, et sur les véhicules lourds on adopta les roues à bandage plein. Cela limitait la vitesse; l'importante hystérésis du caoutchouc, jointe à sa faible conductibilité thermique, conduisait à des températures proches de la fusion du caoutchouc. Pour pallier en partie cet inconvénient, on adopta des roues semi-pneumatiques sur lesquelles le cerclage en caoutchouc était pourvu d'une cavité intérieure appelée « chambre de ventilation ».
Les roues pneumatiques s'avérèrent bientôt comme les seules capables d'amortir efficacement les chocs provoqués par les aspérités de la route : toutefois la faible résistance qui les caractérisait poussa à rechercher de nombreuses solutions de rechange. Parmi celles-ci, les roues élastiques connurent un certain succès. Elles étaient constituées par un cerclage métallique extérieur revêtu de caoutchouc, relié au moyeu par des ressorts à ruban à la place des rais traditionnels: on pouvait ainsi obtenir un certain déplacement élastique du bandage qui présentait les mêmes caractéristiques qu'une roue pneumatique.
Il est intéressant de remarquer que cette solution a été reprise, en version moderne, pour la réalisation des roues du premier véhicule lunaire fabriqué aux États-Unis en 1971. Au début des années dix furent introduites, d'abord en Angleterre, les roues à rayons métalliques qui, étant en deux parties (roue proprement dite et moyeu fixe), permettaient un changement rapide et facile des roues en cas de crevaison. De nombreuses et intéressantes tentatives furent faites pour simplifier la fabrication des roues entièrement métalliques, telles que la roue Sankey, constituée de deux parties en tôle d'acier embouti et soudées entre elles. L'apparition en 1914 des premières roues à voile plein fabriquées par Michelin fut d'une importance capitale; grâce à leur coût peu élevé, elles remplacèrent rapidement les roues à rayons qui, toutefois, continuèrent à être la prérogative des voitures sport.
La solution proposée par Michelin s'avéra si valable qu'elle ne fut plus jamais abandonnée ; même les roues actuelles consistent en un disque métallique embouti en forme conique. pour lui permettre de mieux résister aux contraintes transversales, soudé ou riveté à la gorge de la jante. La première roue fondue en alliage léger fit son apparition, à l'occasion du Grand Prix de France de 1924, sur la Bugatti type 35 : cette innovation, qui avait suscité un grand intérêt pour ses avantages indiscutables, représentés par son faible poids (réduction du moment d'inertie et des masses non suspendues), n'eut pas de suite immédiate en raison de son prix élevé et d'une certaine fragilité. Les Américains furent les premiers à adopter de façon définitive les roues en alliage léger, au début des années cinquante; elles furent montées en Europe en 1957 par Lotus et, en 1958, par Cooper.
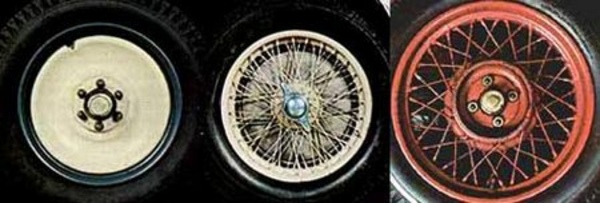
Roue à rayons avec fixation de type Riley (1910 - 1930), roue à rayons type Rudge-Witworth (1930 - 1960), roue tôle à voile plein (1920). D.R.
En 1963 Ferrari, le premier en Italie, adopta finalement les roues en alliage léger pour ses monoplaces et, l'année suivante, également pour ses modèles de série. Ce fut la consécration définitive de cette solution qui s'étendit par la suite à tous les modèles de voitures sportives. Les roues à rayons sont constituées d'une jante reliée au moyeu central par deux ou trois séries de tirants métalliques tendus au moyen de vis spéciales appelées «nipples». Les rayons sont disposés tangentiellement suivant des surfaces coniques à concavités opposées de façon à pouvoir transmettre aussi bien des efforts longitudinaux (de traction ou de freinage) que des efforts transversaux. La fixation de la roue sur la fusée s'effectue au moyen de différents systèmes, les plus courants étant le type Rudge Witworth et le type Riley.
La structure à rayons métalliques présente des avantages au point de vue de l'élasticité de la roue et de la ventilation des freins ; son poids est inférieur à celui d'une roue métallique emboutie uniquement pour les grands diamètres ; pour les petits diamètres, il s'avère par contre souvent supérieur. La construction est assez complexe et coûteuse, de même que l'entretien et le réglage périodique des rayons. Une autre des raisons qui a fait abandonner l'usage de ces roues réside dans l'impossibilité d'adopter des jantes très larges telles que celles utilisées sur les voitures modernes les plus rapides. Les roues à disque sont formées par une jante à gorge soudée ou rivée à un disque embouti d'une forme permettant d'augmenter la rigidité et la résistance aux contraintes transversales. Le voile est en tôle d'acier très doux, d'une épaisseur de 3 à 5 mm, permettant un emboutissage profond.
En général la partie centrale du disque est plus épaisse et est ondulée dans la partie fixée au moyeu pour augmenter la résistance et empêcher un contact total entre le disque et la flasque ; cette précaution permet d'obtenir une réaction élastique du disque sur les goujons de fixation (qui sont au nombre de 3 à 5) et d'éliminer le risque d'un desserrage éventuel, provoqué par les flexions et par les vibrations de la structure de la voiture. Le voile est souvent ajouré, à proximité de la zone, pour réduire son poids et créer, pendant la marche, un flux d'air axial pour le refroidissement des freins. Ce type de roue est le plus répandu à cause de sa résistance, de sa durée et de son faible prix de revient.
Pour clore ce chapitre, on mentionnera un exemple récent de roue en tôle soudée : il s'agit du type de roue fabriqué expressément pour la première version de la Mercedes 630 SEL, voiture réalisée à titre expérimental, en 1969, pour participer aux épreuves de la catégorie Tourisme préparé. Les roues fondues en alliage léger, recherchées surtout pour leur aspect plus esthétique, étant donné la possibilité qu'elles offrent d'obtenir des formes diverses, présentent de gros avantages au point de vue dynamique, qui vont malheureusement de pair avec des prix de revient très élevés.
Si l'on fait abstraction de certains modèles très particuliers, la structure fondamentale de ces modèles reprend celle des roues à rayon avec des tirants de forme trapézoïdale qui consolident la partie du moyeu. Par rapport aux roues à disque en acier embouti, ces roues offrent une diminution de poids et une réduction de 35 % à 50 % environ du moment d'inertie.
La diminution de poids entraîne celle des masses non suspendues, ce qui améliore la tenue de route et soulage le pneumatique pendant les secousses répétées. Le moment d'inertie moins important a une influence négligeable sur l'accélération et le freinage de la voiture, mais diminue de façon notable l'effet gyroscopique qui se produit pendant le braquage et pendant les modifications de carrossage aux vitesses élevées. Une diminution de poids ultérieure a été obtenue, pour les roues destinées aux voitures de compétition, par l'adoption des pneumatiques «tubeless». L'absence de chambre à air a permis de donner à la gorge de la jante une forme en V, de sorte qu'elle se réduit au seul siège des talons du pneu et à son rattachement au moyeu central.
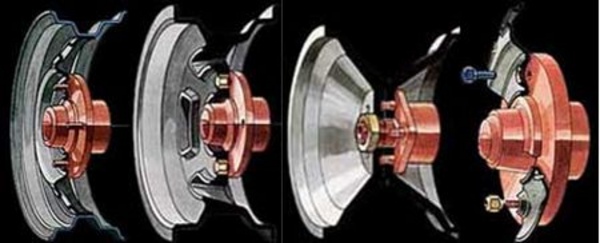
Système de fixation des plus répandus / Le flasque du moyeu est pourvu de trous filetés dans lesquels logent les vis / Fixation rapide sur les voitures de compétition / Dans les voitures de série, le centrage est obtenu grâce à des tétons de centrage ou à un rabat aménagé sur le flasque au niveau du trou central de la jante. D.R.
En cas de choc, les roues en alliage sont plus exposées aux risques d'une rupture que les roues en tôle emboutie qui ne subissent qu'une déformation plastique. De nombreux problèmes techniques sont liés à la fusion des roues. Il est, par exemple, important de veiller à ce qu'il n'existe pas de différences d'épaisseur susceptibles de provoquer des distorsions et des tensions pendant le refroidissement qui suit la fusion; on doit absolument éviter la formation de poches et de bulles de gaz qui, en dehors du risque de déséquilibre dans la distribution des masses, compromettent la solidité des roues.
Les alliages les plus couramment employés sont à base d'aluminium et de magnésium (électron) ; la fusion s'effectue soit au sable, soit en coquille, soit par injection ou par presso-fusion. La fusion au sable offre la meilleure stabilité dimensionnelle et les meilleures caractéristiques mécaniques, mais c'est un procédé long et coûteux qui requiert une série complexe d'opérations pour chaque fusion ; c'est pourquoi ce procédé est utilisé exclusivement pour la fabrication de roues de compétition et, en tout état de cause, pour des séries d'un nombre très limité d'exemplaires.
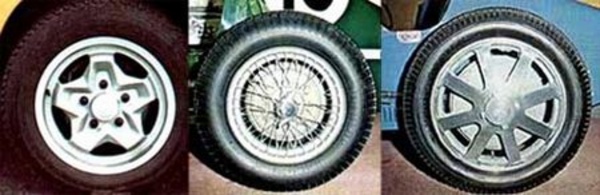
Roue en alliage type Bugatti Grand Prix, roue à rayons type Rudge-Witworth, jante en alliage pour voiture de série. D.R.
La fusion en coquille et la fusion par injection sont, en général, les techniques les plus employées pour les grandes séries destinées aux voitures de série, à cause de leur prix de revient avantageux et de la bonne qualité des pièces fabriquées. La fusion sous pression, par contre, confère à la pièce fabriquée une plus grande fragilité qui doit être compensée par des épaisseurs plus importantes. Ce procédé est assez répandu aux États-Unis.
Une fois fondues, les roues en alliage nécessitent d'importantes opérations d'usinage mécanique telles que l'ébarbage, l'alésage des trous de fixation, l'application de douilles en métal dur aux trous de fixation, le tournage de la gorge et, éventuellement, l'application d'une couche superficielle dans un but à la fois esthétique et protecteur. Elles sont aussi soumises normalement à des contrôles dimensionnels et de poids, et surtout à des contrôles de qualité. où l'on vérifie l'absence de porosités ou de fêlures.
Le diamètre des roues est choisi en fonction du type de véhicule à équiper ou du terrain sur lequel celui-ci devra circuler. Sur les voitures à chevaux. on a toujours adopté des roues arrière de grandes dimensions de façon à obtenir une sensibilité moins accentuée aux aspérités de la route et une vitesse de rotation plus réduite du moyeu. Les roues avant étaient nécessairement d'un diamètre inférieur; la direction à pivot central les obligeait à rentrer sous la caisse du véhicule.
Les automobiles conservèrent longtemps des roues de grand diamètre en raison du très mauvais état des routes. Un facteur déterminant dans le choix du diamètre des roues est représenté par le poids de la voiture ainsi que par le type de terrain sur lequel elle évolue. En augmentant le diamètre, la surface de contact au sol augmente pour une section donnée en même temps que la charge qu'elle peut supporter le même résultat peut toutefois être obtenu en élargissant la section). L'amélioration de l'état et de l'entretien des routes a permis de diminuer le diamètre des roues.
Cette solution présente de nombreux avantages : elle permet en effet d'en réduire le poids et, de ce fait, l'importance des masses non suspendues, tout à l'avantage de la tenue de route ; de réduire le moment d'inertie en permettant de meilleures accélérations pour un couple moteur donné ; d'obtenir des rapports de transmission (engrenages de la boîte de vitesses et de la réduction finale) et des demi-arbres plus légers, grâce au rapport de réduction moins important nécessaire entre la vitesse de rotation du moteur et celle des roues. On constate qu'à une vitesse égale la roue de dimensions inférieures tourne plus rapidement et sa vitesse de rotation est alors plus proche de celle du moteur.
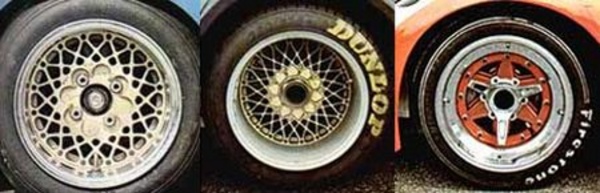
Jante de voiture de série en deux parties; jante en deux parties avec écrou central; jante en trois parties, fixée par un gros écrou central à oreille D.R.
La diminution du diamètre est limitée par la possibilité de charge des pneumatiques et par l'encombrement des freins lorsque ces derniers sont placés directement sur les roues. A ce propos, il faut préciser que le passage des freins à tambour encombrants aux freins à disque, de plus petites dimensions, a permis de réduire de façon non négligeable le diamètre de la jante, et a permis également, à diamètre total égal de la roue, d'adopter des pneumatiques de section supérieure.
Les roues de plus petites dimensions présentent également un certain avantage en ce qui concerne le prix du pneumatique ; leur sensibilité aux déséquilibres aussi bien statiques que dynamiques est moins accentuée.
Il faudra signaler que les pneumatiques de plus petit diamètre, du fait qu'ils accomplissent un plus grand nombre de rotations à parcours égal. seront sujets à une usure plus rapide. Le diamètre des roues varie en général de 500 à 750 mm pour les voitures de tourisme 700 à 1250 mm pour les véhicules industriels: les engins de terrassement ont des roues de grand diamètre, pouvant atteindre 1 500 mm, une mention particulière sera faite pour les roues du camion Terex Titan de General Motors qui; avec un diamètre de 3 mètres, représentent un cas exceptionnel.