Technique : La culasse
le 01/08/2005
La culasse est la partie du moteur qui ferme le haut des cylindres et dans laquelle s'effectue la combustion. En général, les soupapes d'admission et d'échappement y sont logées. Sa forme et ses caractéristiques ont toujours été étroitement liées à l'évolution des moteurs et ont été plus particulièrement déterminées en fonction du type de distribution et de la forme de la chambre de combustion.
Les premières culasses
Bien que quelques-uns des premiers moteurs d'automobile aient été équipés d'une culasse séparée du bloc-cylindres, la majorité des constructeurs préférait alors la culasse solidaire du bloc- cylindres. Cette solution permettait d'obtenir des pièces plus résistantes et évitait le planage des surfaces de contact (culasse/bloc-cylindres), en éliminant ainsi tous les problèmes d'étanchéité.
En ce qui concerne la distribution, on utilisa, sur les premiers moteurs à gaz, des soupapes latérales : c'est-à-dire disposées de chaque côté du cylindre. Les vitesses et les pressions toujours croissantes des moteurs conduisirent, pour éviter des difficultés d'usinage, à adopter des soupapes d'admission automatiques commandées par la dépression créée pendant l'admission dans le cylindre.
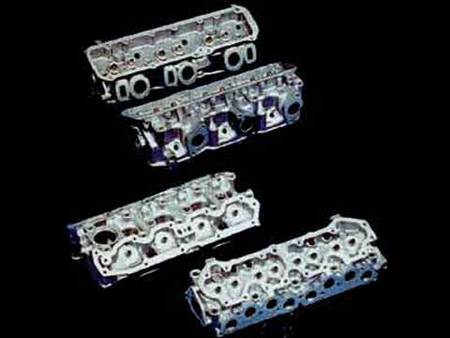
D.R.
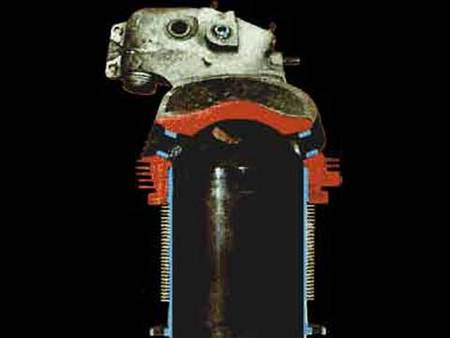
Ancienne culasse vissée D.R.
Cependant, avec l'augmentation des vitesses de rotation, ce système se révéla peu efficace. Le rappel de la soupape étant commandé par un ressort, une partie importante de la course d'admission était annulée pour permettre de créer une dépression capable de vaincre la force de celui-là. On en arriva donc aux soupapes d'admission commandées.
Les systèmes de commande des soupapes étaient souvent placés en dehors de la culasse et exposés à l'air, ceci afin d'assurer un meilleur refroidissement ou encore un entretien plus facile.
En effet, l'action de martèlement de la soupape sur son siège provoquait une diminution du jeu dans la commande de la distribution, et, à cette époque, un réglage au moins du jeu des poussoirs était nécessaire par journée d'utilisation. Ceci explique pourquoi les rendements, les pressions spécifiques et le régime de rotation du moteur restaient particulièrement bas. Le dessin des culasses, conçu de façon à faciliter l'entretien du moteur, imposa la disposition des soupapes latérales de chaque côté du bloc, commandées par deux arbres à cames différents.
Cette solution, qui avait l'inconvénient de provoquer une répartition non uniforme de la température - créant un côté froid et un côté chaud - provoquait des déformations.
Pour cette raison, on adopta bientôt des chambres en L avec les deux soupapes du même côté ; la bougie étant placée à proximité de la soupape d'admission pour être refroidie par le mélange aspiré, quand les culasses n'étaient pas séparées du bloc-cylindres, l'accès aux soupapes se faisait à travers des bouchons filetés en laiton ou en bronze, ce qui avait pour conséquence, à l'échappement, de créer des points chauds dans ces zones.
Pour obtenir un refroidissement plus efficace, dans les moteurs à refroidissement par air, les bouchons étaient conçus en alliage léger et munis d'ailettes.
Disposition des soupapes et rendement
L'adoption définitive de la culasse démontable élimina ces bouchons et permit d'étudier avec une plus grande précision la forme de la chambre de combustion pour améliorer le rendement. Parmi les formes donnant un rendement appréciable, la culasse conçue par Ricardo, aux environs de 1920, s'imposa- Tout en conservant des soupapes latérales, elle permettait d'obtenir un rapport volumétrique relativement élevé et une bonne turbulence.
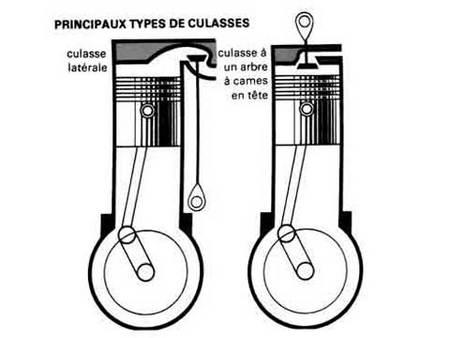
D.R.
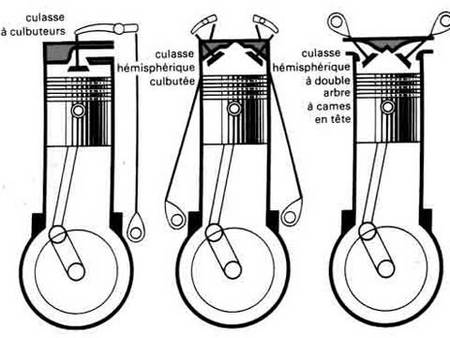
D.R.
Le stade suivant fut marqué par l'éloignement des deux soupapes l'une de l'autre, de façon à éviter le transfert de chaleur des gaz d'échappement au mélange frais.
On vit également apparaître quelques moteurs présentant une solution intermédiaire : soupapes d'admission en tête et soupapes d'échappement latérales (disposition conservée jusqu'à une époque relativement récente sur les Rolls Royce, Bentley et Rover).
Les culasses à soupapes latérales logées dans le bloc-cylindres ne permettaient pas d'atteindre des régimes supérieurs à 4000 tr/mn, surtout cause de la forme peu heureuse des conduits.
Bientôt les soupapes en tête culbutées s'imposèrent. Pour des raisons de facilité d'usinage, les soupapes en tête furent tout d'abord placées côte côte parallèlement à l'axe des cylindres, disposition qui ne permettait pas l'utilisation de soupapes de grandes dimensions, les moteurs ayant général une course longue et un alésage réduit.
Afin de pouvoir augmenter leur diamètre, chambre de combustion fut élargie jusqu'à atteindre des dimensions supérieures à celles de l'alésage.
Au cours des années soixante, la distribution arbre à cames en tête, avec commande directe des soupapes, s'est imposée progressivement, même pour la grande série.
Cette solution offre sans conteste des avantages du point de vue du rendement global du moteur mais présente une plus grande difficulté d'usinage pour la réalisation de la culasse, qui est souvent fabriquée en deux parties séparées : le support et l'arbre à cames et la culasse proprement dit.
Étude et fabrication d'une culasse
Au cours des années soixante-dix, les problèmes créés par la pollution atmosphérique et les normes auxquelles ont été soumis les moteurs automobiles, ont accru les difficultés de fabrication. Il suffit de citer à titre d'exemple le moteur conçu par Honda et prévu pour dépasser, en 1976, les standards américains.
Ce moteur, appelé CVCC (Compound Vortex Controlled Combustion) est du type à turbulence contrôlée ; il comporte deux chambres de combustion séparées, l'admission s'effectuant simultanément par les deux soupapes. Dans l'étude d'une culasse destinée à un moteur à combustion interne moderne, on s'efforce d'atteindre trois buts principaux : un bon rendement, un niveau de pollution très bas et un prix de revient très faible.
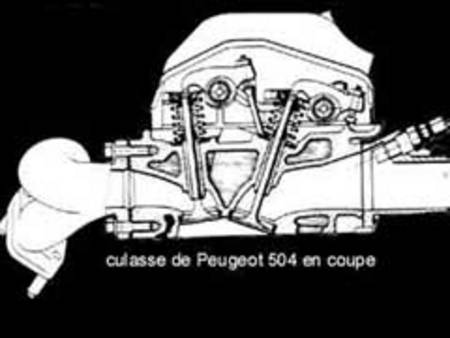
Coupe de culasse de Peugeot 504 D.R.
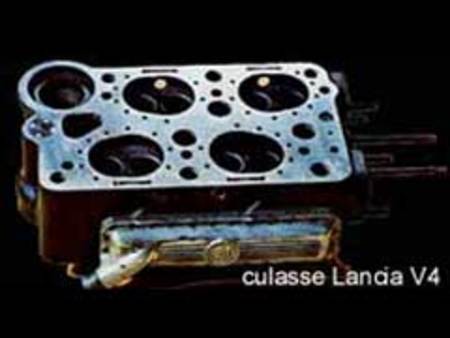
Culasse de Lancia V4 D.R.
Ces trois objectifs ne sont pas toujours compatibles. Mais on peut penser qu'en ce qui concerne les normes antipollution, elles ne conduiront pas nécessairement à sacrifier le rendement du moteur et sa puissance maximale.
En général, on étudie la forme et l'inclinaison des conduits d'admission et d'échappement de façon à créer la plus grande turbulence possible dans la chambre de combustion sans toutefois diminuer la vitesse d'introduction des gaz, donc le taux de remplissage.
Il faut veiller plus particulièrement à ce que la section transversale des conduits conserve dans toute sa longueur un diamètre constant, ou qu'elle n'accuse qu'une conicité négligeable. Les dimensions et la forme de la chambre de combustion dépendent du rapport course-alésage.
Le problème de la pollution semble justement favoriser aujourd'hui un retour au moteur à course longue, c'est-à-dire avec des chambres d'explosion compactes (ce qui réduit le diamètre des soupapes).
On considère en général que la surface de la soupape d'échappement doit être égale à environ 60 à 80 % de celle de la soupape d'admission. Dans le cas de moteurs à rendements élevés, on a souvent recours à une solution complexe consistant à adopter trois ou quatre soupapes par cylindre.
En effet, la section effective du passage de deux soupapes de petites dimensions est nettement supérieure à celle d'une seule ayant une surface égale à la somme de deux autres de diamètre inférieur.
Étant donné que presque tout l'espace disponible de la chambre d'explosion est utilisé pour loger les soupapes dans les meilleures conditions, il ne reste qu'une marge très réduite pour la bougie, qui doit être placée surtout en tenant compte de son accessibilité pour le démontage.
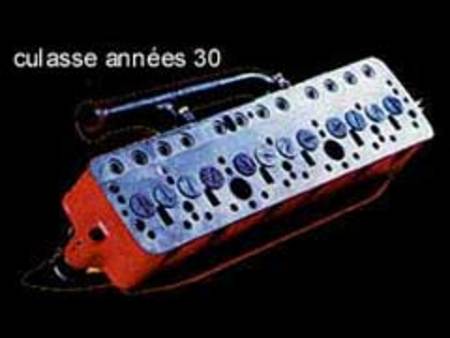
Culasse des années 30 D.R.
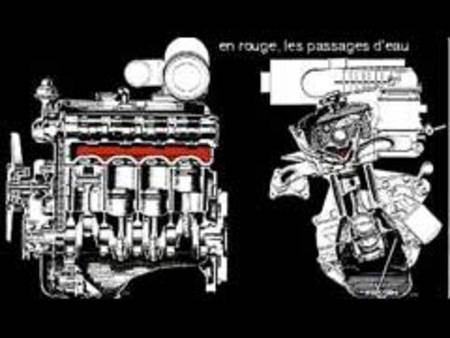
En rouge : les passages d'eau D.R.
Signalons aussi que, souvent, la forme de la chambre est conditionnée par les exigences de l'usinage et la nécessité de réaliser une économie dans sa fabrication. Ainsi, pour simplifier la culasse de l'Alfa Romeo Alfasud, on lui a donné une forme absolument plate, les chambres de combustion étant entièrement creusées dans les pistons.
Après avoir arrêté les dimensions des conduits et de la chambre de combustion, le constructeur choisit le type de distribution, problème lié en général à des considérations d'ordre économique.
La solution de l'arbre à cames en tête complique énormément la fonderie.
Dans ce cas, la culasse est souvent composée de deux parties :
- la partie inférieure, qui comprend la chambre de combustion, les conduits d'admission et d'échappement, et les soupapes ;
- la partie supérieure, qui comprend les supports de l'arbre à cames et les guides de soupapes.
Un soin particulier doit être apporté ; l'étude des canalisations de refroidissement soit pour simplifier l'usinage des chemisages intérieurs. soit pour obtenir un échange thermique efficace et pour éviter la formation de points chauds dans la culasse (risques de déformation ou de pré allumage).
Les mêmes considérations sont valables pour l'étude des conduits de graissage des culbuteurs et des paliers de l'arbre à cames en tête. Le retour de l'huile dans le carter s'effectue le long des goujons de fixation de la culasse, ou encore à travers des canalisations de réception spéciales.
Matériaux et procédés de fabrication
Les culasses sont réalisées en fonte ou en alliage d'aluminium. Sur les moteurs modernes on préfère, en général, utiliser les alliages légers soit à cause des avantages importants qu'ils présentent au point de vue de la réduction du poids, soit à cause de leurs excellentes caractéristiques de fusion et de transmission thermique.
Les supports de la distribution sont en général réalisés par le processus de fonderie sous pression, qui permet de fabriquer des pièces d'une finition parfaite, avec des parois très minces.
La partie inférieure de la culasse est obtenue par coulage en coquille ou, plus rarement, par coulage dans des moules en sable ; elle est réalisée en fonte, dont la composition est adaptée au matériau employé pour les soupapes, de façon à éviter tout risque de grippage.
Pour les culasses en alliage léger, on utilise des guides en bronze, qui s'adaptent mieux aux dilatations du matériau. Les sièges des soupapes sont également mis en place à la presse ; ils sont fabriqués en fonte ou en acier, avec un apport éventuel (stellite) de matériau résistant aux températures élevées et à la corrosion.
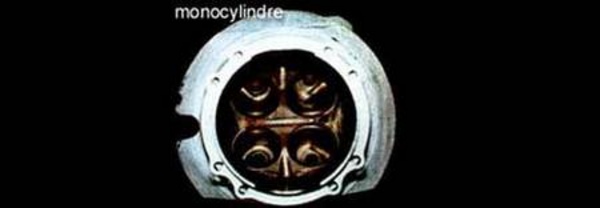
D.R.
Pannes et défauts
Les inconvénients pouvant provenir d'un processus de fabrication imparfait sont nombreux. Par suite d'une fonderie défectueuse, les culasses peuvent présenter des criques ou des porosités.
Les criques sont causées par des phénomènes anormaux de réaction interne du matériau dus à des erreurs dans l'établissement du projet de la pièce ou par un mauvais refroidissement du moule. Les soufflures, ou porosités, étant dues en général aux mauvaises caractéristiques de l'alliage, sont des imperfections qui se vérifient dans la coulée.
Dans les deux cas, il peut se produire, en cours d'utilisation de ces pièces, des infiltrations d'eau dans l'huile ; ces défauts (très rares) nécessitent en général le remplacement de la culasse.
Sur les moteurs modernes, un autre défaut, imputable à l'usinage mais également très rare, est constitué par un planage défectueux des surfaces de la culasse et du bloc-moteur. Des suintements d'huile ou d'eau peuvent également se produire dans ce cas et provoquer facilement la détérioration du joint de culasse.
D'autres défauts proviennent, par contre, d'un mauvais entretien, ou sont la conséquence d'incidents affectant d'autres parties du moteur.
En général, sur tous les moteurs modernes neufs, il est nécessaire de contrôler et de régler les écrous des culasses après un parcours de 1500 à 2 000 km. Cette même opération est indispensable après chaque révision du moteur à la suite du remplacement d'un joint de culasse, pour compenser son écrasement.
Le resserrage doit être exécuté sur un moteur froid, au moyen d'une clé dynamométrique, en plusieurs passes correspondant chacune à un couple et selon l'ordre de serrage prévu par le constructeur. Pour éviter une erreur de lecture, provoquée par le décollement du boulon, il est nécessaire, après avoir effectué le premier serrage, de desserrer les écrous d'un quart de tour et de les serrer à nouveau au couple prévu par le constructeur. Après cette opération, une vérification du jeu des poussoirs est nécessaire. Un mauvais serrage des écrous de la culasse peut provoquer des déformations (plus fréquentes sur les culasses en fonte). Le même inconvénient peut se produire par suite d'une surchauffe (manque d'eau), d'un fonctionnement défectueux du thermostat, ou encore de la rupture de la pompe à eau ou du ventilateur, etc.
Pour contrôler la planéité de la culasse, après avoir démonté les soupapes, il faut disposer d'un marbre de contrôle que l'on enduit de noir de fumée ou de sanguine et sur lequel on la fait glisser. Si la surface présente des zones colorées irrégulières, il est nécessaire de procéder à sa rectification (au maximum 0,2 mm).
Autre inconvénient caractéristique, qui se vérifie après un assez long kilométrage : l'usure progressive des soupapes et de leurs sièges, plus particulièrement ceux des soupapes d'échappement corrodés par les gaz brûlés. De même, les guides peuvent se gripper, ou accuser un jeu compromettant l'étanchéité des soupapes elles-mêmes.
L'utilisation prolongée du moteur provoque également, dans la chambre d'explosion, des dépôts de calamine qui ont une influence sur son rendement et peuvent empêcher la fermeture parfaite des soupapes.
Dans tous ces cas, le rendement du moteur est imparfait, en particulier quand, pour des motifs divers, l'étanchéité des soupapes n'est plus totale, il se produit des difficultés pour le départ à froid, des explosions irrégulières, ainsi que des retours de flamme, le moteur ne tient pas le ralenti, ou boîte, etc. Pour toutes ces éventualités, il est nécessaire de procéder à une révision de la culasse.